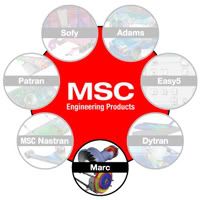
Summary
Finite element analysis (FEA) is a critical part of the virtual design process. But because most FEA programs are linear, they can only study parts that deform a small amount, certainly not enough to ......
Specs
Manufacturer - MSC Software Corporation
Software Type - Finite element analysis (FEA)
Language - English
System Requirements -
Features
• Simulate real-world problems involving contacts and nonlinear material effects.
• Reduce the time and cost required to get your new products to market by using simulation instead of the traditional build-and-break process.
• Increase your confidence in the final product by virtual testing it under all conceivable loading conditions
Download Link ......
5 comments:
Finite element analysis (FEA) is a critical part of the virtual design process. But because most FEA programs are linear, they can only study parts that deform a small amount, certainly not enough to deformation to exceed the linear elastic range of the materials.
Finite element analysis (FEA) is a critical part of the virtual design process. But because most FEA programs are linear, they can only study parts that deform a small amount, certainly not enough to deformation to exceed the linear elastic range of the materials.
But Marc has no such limitations. A nonlinear FEA program, Marc enables you to assess the structural integrity and performance of parts undergoing large permanent deformations as a result of thermal or structural load. The types of deformations the program can study include geometric nonlinearities (metals bending) and material nonlinearities (elastomers and metals that yield under structural or thermal loading). You can also use Marc to simulate deformable, part-to-part or part-to-self contact under varying conditions that include the effects of friction—critical for analyzing nonlinear behavior in tool-and-die set-up, spring coil clash, or a windshield wiper system.
And whether you are designing with glass, rubber, steel, or concrete, Marc offers an extensive library of metallic and non-metallic material models, along with a library of 175 elements for structural, thermal, and fluid analysis.
Combine with pre- and post-processors
You can drive all Marc products through the common GUI offered by Patran or Marc Mentat, two pre- and post processors that work with Marc. Mentat also provides the unique ability to process large problems in parallel using the domain decomposition technique. Loading conditions can originate from physical tests or virtual tests using Adams. MSC Software AFEA is a bundled version of Patran and Marc.
Marc Applications
• Manufacturing Processes: metal-forming, welding, cutting, bending, extruding, fastening, crimping, tooling, component assembly
• Metallic Structures & Components: cables and wires, plates, panels, frames, sheets, rods, micro-electromechanical systems (MEMS), biomechanical stents and other implantable surgical devices, mechanical-hydraulic connectors
• Elastomeric Materials & Components: rubber, plastic, gaskets, seals, hoses, belts, shock absorbers, vibration-isolation mounts and bearings, bushings, tires, constant velocity (CV) joint boots, windshield wipers, weatherstripping
• Contacting & Self-Contacting Parts: tire-to-wheel rim, gasket-to-engine block, seal-to-door, gear tooth-to-tooth, CV boot self-contact, struts, axles, connectors, crimps, fasteners, snap-fit mechanisms, child-safety caps, electromechanical connectors
• Load-Carrying Analyses: buckling, creep, cracking, failure and safety analysis
• Coupled Thermal-Structural Interactions: engine block components, disc brakes, radiators, heat sinks, glass forming, nuclear plant pressure vessels and piping, gas turbine components
Application Briefs
When F is not = Ku : An Introductory Guide to Nonlinear Analysis
Nonlinear FEA of Elastomers Technical Paper
Marc Modules
MSC.Marc Mentat
What's New: Marc 2007 r1
The Marc Product Family provides the most comprehensive and advanced Nonlinear Finite Element Analysis (FEA) solution available to support the successful application of Virtual Product Development (VPD). Customers continue to be our close partners for developing unique VPD solutions, reinforcing our strategy and commitment to offer complete structural, thermal, and coupled analysis capabilities that will meet their current and future needs for a wide range of engineering applications and manufacturing processes. Each new release of Marc includes new functionality and enhancements to improve usability, performance, quality, and robustness.
A general description of each of these new capabilities is listed below. For more details on these and many other enhancements, please refer to the Marc 2007 r1 Release Guides on the Marc Technical Support Website.
New element and material models, including interface elements, cohesive material models and MSC Nastran (NLELAST) capability to model nonlinear stress-strain curve. The new elements in Marc 2007 r1 release include heat transfer and structural elements, interface elements to used to simulate onset and progress of delamination as well as solid-shell element useful in double-sided contact applications.
Sheet Metal Forming with Solid-Shell Element
More new composites failure criteria including Hashin, Puck and other failure criterion.
Advanced Thermal capabilities including aerodynamic heating, QVECT (thermal vector flux), convection to node and others. Extends Marc's usability though support of MSC Nastran thermal capabilities and facilitate Marc and MSC Nastran integration. Shown below are radiation tests with new heat transfer membrane elements.
VCCT (Virtual Crack Closure technique) for crack initiation and propagation : A simple but general way to evaluate energy release rate of a crack. VCCT can be used to simulate dynamic crack growth in 2D (with adaptive meshing support) and 3D (via contact ungluing).
Another new feature in Marc 2007 r1, the Cohesive Zone Modeling for delamination provides a technique to simulate physical separation of different materials or crack growth in a single material. Bilinear, exponential and similar cohesive material models have been implemented to simulate onset and progress of delamination.
Enhancements to global adaptive meshing for shell re-meshing with loads and boundary conditions, user defined mesh generator and much more. Shown below are examples of global re-meshing of shells – deep drawing by 3-node thin shells and twisting by 4-node thick shells.
Marc® 2007 r1 Tech Sheet
Product Family
Marc®
MODELING METHODS
Finite Element Library
Marc has over 200 elements that are available for structural, thermal, electrical, electrostatic, magnetostatic, electromagnetic, acoustic, bearing, diffusion, and fluid analysis. These elements are state-of-the-art, robust, accurate, and can handle large displacements, large rotations, and finite strains.
Cable, Truss, Beam
Plane Stress and Strain
Generalized Plane Strain
Axisymmetric
Plate, Membrane, Shell
Large Rotation, Reduced Integration Shell
3-D Solid
Incompressible (Herrmann)
Rebars (Continuum and Membrane)
User-Defined Elements
Special Elements
Gaps
Pipe-Bend
Elbow
Rigid
Gasket
Semi-Infinite
Shear Panel
Composite (Shell, Solids)
Cavity (2-D, 3-D, Axisymmetric Surfaces)
3-D Current Carrying Wire for Magnetostatics
Interface Elements
Solid-Shell element
Wire elements for Electromagnetics
Material Models
Marc has an extensive library of metallic and non-metallic material models, which allows the representation of virtually any material ranging from simple linear elastic materials to complex time- and temperature-dependent materials.
Linear-Elastic
Isotropic, Orthotropic, and Anisotropic (Temperature-Dependent)
Elastic-Plastic
Isotropic, Kinematic, or Combined Hardening
von Mises Yield Criterion
Drucker-Prager Yield Criterion
Oak Ridge National Laboratory Model
Analytical Hardening Behavior Models (Additive Power Law, Cowper-Symonds, Multiplicative Power Law, Kumar, and Johnson-Cook)
Strain-Rate Effects
Hill's Anisotropic Plasticity
Barlat Anisotropic Plasticity
Temperature-Dependent Properties
Gurson Damage Model for Metal Plasticity
Chaboche Viscoplastic Model
Finite Strain (Additive Decomposition or Multiplicative Decomposition [FeFp])
Forming Limit Data for Sheet Forming Limit Diagrams
Grain Size Prediction
Elastomers
Large-Strain Viscoelastic Model
Nonlinear Elastic in Total or Updated Lagrange Framework
Generalized Mooney-Rivlin Model
Ogden Model
Boyce-Arruda Model
Gent Model
Foam Model (Large-Strain Compressible)
Elastomer Damage and Fatigue
Hypoelastic
Rigid-Plastic Flow
Fast Sheet Metal Forming Analysis
Plane Stress Option
Super Plastic Forming Simulation
Creep
Deviatoric or Volumetric Strains
Volumetric Swelling
Piecewise-Linear or Exponential Rate of Equivalent Creep Strain
Temperature Dependent
ORNL Model (Combines Creep, Plasticity, and Cyclic Loadings)
Implicit Creep With Plasticity
Viscoelasticity
Maxwell and Kelvin Models
Hereditary Integrals Formulation for Small and Large Strains
Thermo-Rheologically Simple Behavior
Narayanaswamy Viscoelastic Thermal Expansion
Isotropic and Anisotropic Materials
Viscoplasticity
Combined Plasticity and Maxwell Creep Mode
Powder Metallurgy
Viscoplastic Model of Powder Materials
Hot Isostatic Pressing Process
Temperature and Density Changes
Shape Memory
Mechanical model for super-elastic materials
Thermo-mechanical model for superelastic and shape memory materials
Conversion between Mechanical and Therm-mechanical Models
Cohesive Material Models
Bilinear
Exponential
Composites
Laminated Plates, Shells, and Solids
Elastic-Plastic Behavior
Arbitrary Material Orientations
Relative Ply Angle for Each Layer
Fast integrated composite shells
Multiple Failure Criteria ( Maximum Stress, Maximum Strain, Tsai-Wu, Hill, Hoffman, Hashin, Puck, Hashin-Tape, Hashin-Fabric or User-Defined)
Progressive Failure
Heat Transfer Analysis
Gasket Material for Thermo-Mechanical Analysis
Soils and Poro-Plasticity
Yield Surfaces as a Function of Hydrostatic Stress
Linear or Parabolic Mohr-Coulomb Law
Fully-Coupled Fluid-Solid Soil Problem
Modified Cam-Clay Model
Concrete
Low-Tension, Cracking, Crushing Surfaces
Piezoelectric
Isotropic or Orthotropic
Magnetostatics
Nonlinear B-H Relation
Permanent Magnets
Rebars
Micro-Buckling Behavior for Rebar Elements
Nonlinear stress-strain curve
Nastran (NLELAST) capability to model nonlinear stress-strain curve
Hypoelastic
Principal stress based model
Bi-modulus linear elasticity
Bi-modulus linear elasticity with cut-off
Nonlinear orthotropic elastic model
Table Input
This new capability allows for a completely new way of controlling the load and initial and boundary condition history, as well as defining material properties, in Marc. Table Input is available in Marc, Mentat, and Patran.
May be Applied to Load, Initial, and Boundary Conditions
Surface-Dependent Pressure Loads
Motion of Rigid Contact Bodies
Time-Dependent Point Loads
Variable Spring Constants
Variable Weld Heat Source Velocity
May be Applied to Virtually All Material Properties
Up to Four Simultaneous Independent Variables
Over 50 Independent Variable Types
Original or Deformed Coordinates
Time, Frequency, Increment
Pressure, Temperature, Stress, Strain
May be Defined by a Mathematical Equation
Table Data or Equation Evaluated Directly During Solution
Analysis Boundary Conditions
Mechanical
Thermal
Joule
Acoustic
Electrostatic
Magnetostatic
Electromagnetic
Fluid
Bearing
Diffusion
State Variables
Geometrically Applied Boundary Conditions
General Section Constraint for Bolt Modeling
Pre-State
Transfer Axisymmetric to 3-D
Transfer 2-D Plane Strain to 3-D
Transfer 2-D Generalized Plane Strain to 3-D
Nodal Transformation
MPCs (Multi-point constraints)
Nodal Ties
Servo Links
Spring/Dashpots
RBE2
Large Rotation RBE3 Constraints
Inserts
Auto- M set
Connector elements
CWELD and CFAST (point-point, point-patch and patch-patch connections)
CBUSH (general nonlinear spring/damper)
Global-to-Local Zooming
2-D Solid 2-D Solid
3-D Solid 3-D Solid
3-D Shell/Membrane 3-D Shell/Membrane
3-D Shell/Membrane 3-D Solid
Welding
Control of Weld Path
Control of Fill Material
Machining
Elements Removed via CAD/NC Data
Automatic Remeshing/Deactivation of Elements in Cutter Path
Pre-State for Initial Stress Conditions (Residual Stresses)
Visualization of the Machining Process Results
Contact
2-D and 3-D Contact
Discrete or Analytical Rigid Contact Surfaces
Continuous Normals Using Spline and Coons Surfaces
Automatic detection of discontinuities
Optimized Contact Detection
Ability to Use Higher-Order Elements
Beam-to-Beam Contact
Cyclic Symmetry
Load/Velocity/Position-Controlled Rigid Bodies
Friction Models (Coulomb, Shear, and User-Defined)
Arctangent, Stick-Slip Friction Models and Bilinear Friction Model
Interference-Fit Calculations
Dynamic Impact
Stress-Free Initial Contact
Delayed slide-off
Thermal Contact
Near Thermal Contact Allows for Both Convection and Radiation
Possible with Transformed Nodes
Electrostatic-Structural
Diffusion
Radiation
Adding/Changing Rigid Surfaces During Analysis
Automatic handling of MPC constraints in combination with contact
SOLUTION METHODS
Marc uses the latest proven numerical analysis techniques with all calculations performed in double precision for maximum accuracy. Optimization procedures substantially reduce memory requirements and improve computational performance for linear and nonlinear problems.
Linear
Superposition of Load Cases
Fourier (Asymmetric) Analysis of Axisymmetric Bodies, including Shells
Nonlinear
Adaptive Load/Time Control (Static, Post-Buckling, Dynamic, Creep, and Heat Transfer)
AUTO STEP Capabilities:
Convergence Automation
Automatic Time-Step Reduction
Arc-Length Methods
User-Controlled Load/Time-Stepping
Automatic Damping for Stability
Inertia Relief
Large Deformation and Finite Strain
Total and Updated Lagrange Procedure
Buckling (Linear and Nonlinear)
Creep Buckling
Post-Buckling with Adaptive Load-Step
Perturbation Buckling
Finite Strain Plasticity
Global Adaptive Meshing
2-D (Lower-Order Quad and Tri) Automatic Remeshing with loads and boundary conditions
3-D (Lower-Order Tetrahedral and Hexahedral) with loads and boundary conditions
Remeshing Criteria Based on Increments, Penetration, Element Distortion, or Instructed Request
Adaptive Refinement Based on Curvature
Advanced Meshing Technology Including Overlay, Advancing Front, and Delauney Triangulation
Remeshing of Multiple Deformable Bodies
Shells remeshing with loads and boundary conditions
User defined mesh generator
Material particle flow tracking
Local Adaptive Meshing
Linear and Nonlinear Analysis
Choice of Multiple Adaptive Criteria
Special Capability for Contact Analysis
Structural and Heat Transfer Analysis
Mesh Refinement and Mesh Consolidation
Dynamics
Eigenvalue Extraction (Inverse Power Sweep and Lanczos)
Transient Response
Modal Superposition
Direct Integration:
Generalized Newmark Operator
Houbolt Operator
Single-Step Houbolt Operator
Explicit Dynamics (Central Difference Operator)
Harmonic Response
Spectrum Response
Time-Stepping (Fixed or Adaptive)
Consistent or Lumped Mass Matrix
Interface to ADAMS via Creation of MNF both Linear and Pre-Stress Analysis
Heat Transfer
Steady-State and Transient
Conduction (Linear and Nonlinear)
Convection (Radiation Boundary Conditions)
Latent Heat and Phase Changes
Adaptive Time Steps
Radiation View Factors for 2-D, Axisymmetric, and 3-D Cavities
Monte Carlo Method Computed by Marc Mentat
Hemi-Cube Projection Method Computed by Marc
2-D Planar, Axisymmetric, Shells, 3-D Solids
Global Remeshing and Adaptive Meshing in 2-D
View Factor Magnitudes can be Visualized
Thermo-Mechanical
Quasi-Coupled, Thermally-Driven Stress Analysis
Fully-Coupled Thermo-Mechanical Analysis
Heat Generated by Plastic Deformation and Friction Effects
Large Displacement Effects on Thermal Boundary Conditions
Advanced Thermal capabilities
Aerodynamic heating
QVECT (thermal vector flux load)
Convection to node
Channel and Conrad gap table support
Thermal equilibrium
Fracture Mechanics
Linear and Nonlinear
Brittle and Ductile Models
J-Integral (Static and Dynamic Calculations)
Virtual Crack Closure Technique (VCCT)
Adaptive meshing support (2D)
Crack propagation (2D and 3D)
Steady-State Tire Analysis
Fluid Analysis
Navier-Stokes Equations in 3-D
Mixed Method or Penalty Approach to Satisfy Incompressibility
Newtonian or Non-Newtonian Fluid
Fluid-Thermal Coupled Analysis
Fluid-Solid Coupled Analysis
Fluid-Thermal-Solid Coupled Analysis
MpCCI Support
Hydrodynamic Bearing
Lubrication Problems
Pressure Distribution and Mass Flow
Acoustics
Rigid Reflecting Boundaries
Eigenvalue and Transient Analysis
Coupled Deformable Structural-Acoustic Analysis
Joule Heating
Coupled Electric Flow with Heat Transfer
Coupled Electrical-Thermal-Mechanical Analysis
Diffusion Simulation
Electrostatics
2-D and 3-D Scalar Potential
Electrostatic-Structural Coupling
Magnetostatics 2-D and 3-D Vector Potential
Nonlinear B-H Relations
Permanent Magnets
Piezoelectric Analysis
2-D and 3-D Modal, Harmonic, or Transient Response
Electromagnetics
Fully-Coupled Maxwell Equations
Harmonic and Transient Analysis
Coupled Electromagnetics-Thermal
Computational
Efficient Direct and Iterative Solvers
In-Core and Out-of-Core Capabilities
Restart
True 64-bit capability
Parallel Processing
Available for Most Analyses
Domain Decomposition in Preprocessor (MSC.Marc Mentat or MSC.Patran)
Single Input File (Domains Decomposed in MSC.Marc)
Available for Local Adaptive Meshing
Integration
DMIG Support
Nonsymmetric DMIG support
Streaming input
Common component and modules for Nastran
USER SUBROUTINES
This powerful feature enables the user to run customized subroutines in place of the pre-existing ones in Marc, providing the user with wider latitude for solving nonstandard problems.
User-Defined Elements
Material Behavior
Boundary Conditions
State Variables
Geometric Modifications
Input/Output Modifications
PRE- AND POSTPROCESSING WITH MENTAT
Mentat is tightly integrated with Marc to facilitate preprocessing, postprocessing, and analysis submission and control.
CAD Import
Geometry Model Creation
Mesh Generation
Material Definition
Modeling Tools
Transformations
Cavities
Matching Boundaries (Bolts)
Chains
Sink Point Groups
Streamline Regions
Fracture Mechanics
Welding (Paths & Fillers)
Contact Body Definition
Links
Initial Conditions
Boundary Conditions
Mesh Adaptivity
Global Remeshing
Local Adaptive Meshing
Analysis Job Initiation, Monitoring, and Control
Results Visualization and Postprocessing
USER DOCUMENTATION
Users have instantaneous access to the extensive Marc online documentation, which includes hyperlinks between topics, a search engine, and detailed illustrations and examples.
MSC.Marc User's Guide
Installation Guide
Release Guide
Python Tutorial and Reference Manual
Volume A: Theory and User Information
Volume B: Element Library
Volume C: Program Input
Volume D: User Subroutines and Special Routines
Volume E: Demonstration Problems
Part I: Linear
Part II: Plasticity and Creep, Large Displacement
Part III: Heat Transfer, Dynamics
Part IV: Fluids, Design Sensitivity & Optimization, NAFEMS
Part V: Verification
HARDWARE PLATFORM SUPPORT
Marc routinely solves large, computationally intensive problems by taking advantage of parallel processing architectures and other hardware platform improvements to achieve highly scalable, linear speed improvements on dedicated machines. Marc is supported on shared and distributed memory machines and workstation clusters running under a variety of UNIX, Windows NT, and Linux operating systems.
HP-Alpha (DEC), Tru64 5.1
HP (64-bit), HPUX 11.0
HP (64-bit), HPUX 11.23 IBM (64-bit), AIX 5.2
SGI (mips4 64-bit), IRIX 6.5
SGI (Altix 64-bit), Linux 2.4.21-sgi303r2
Sun (64-bit), Solaris 2.8
Linux (32-bit), RedHat 9
Linux (64-bit), RedHat AS 3.0
Linux (64-bit), RedHat WS 3.0
Intel (32-bit), Windows 2000
Intel (64-bit), Windows Server 2003 x64
More details of the hardware platform support can be obtained from the Hardware and Software Requirements guide on the product support page.
USER TRAINING AND TECHNICAL SUPPORT
MSC.Software offers a variety of technical support resources, including training, hotline support, software and documentation updates, and consulting services. For more information, please visit: http://www.mscsoftware.com/support/prod_support/marc
Post a Comment